
The controller can adjust suitable parameters effectively, and the real-time speed track the target rapidly. In this paper, auto-tuning PID controller is applied to analyse the system output response in time domain with varying speed and load conditions. PID auto-tuning algorithm includes trial and error method, critical proportion method, attenuation curve method, response curve method, relay feedback method, self-tuning, pattern recognition method, and so on.
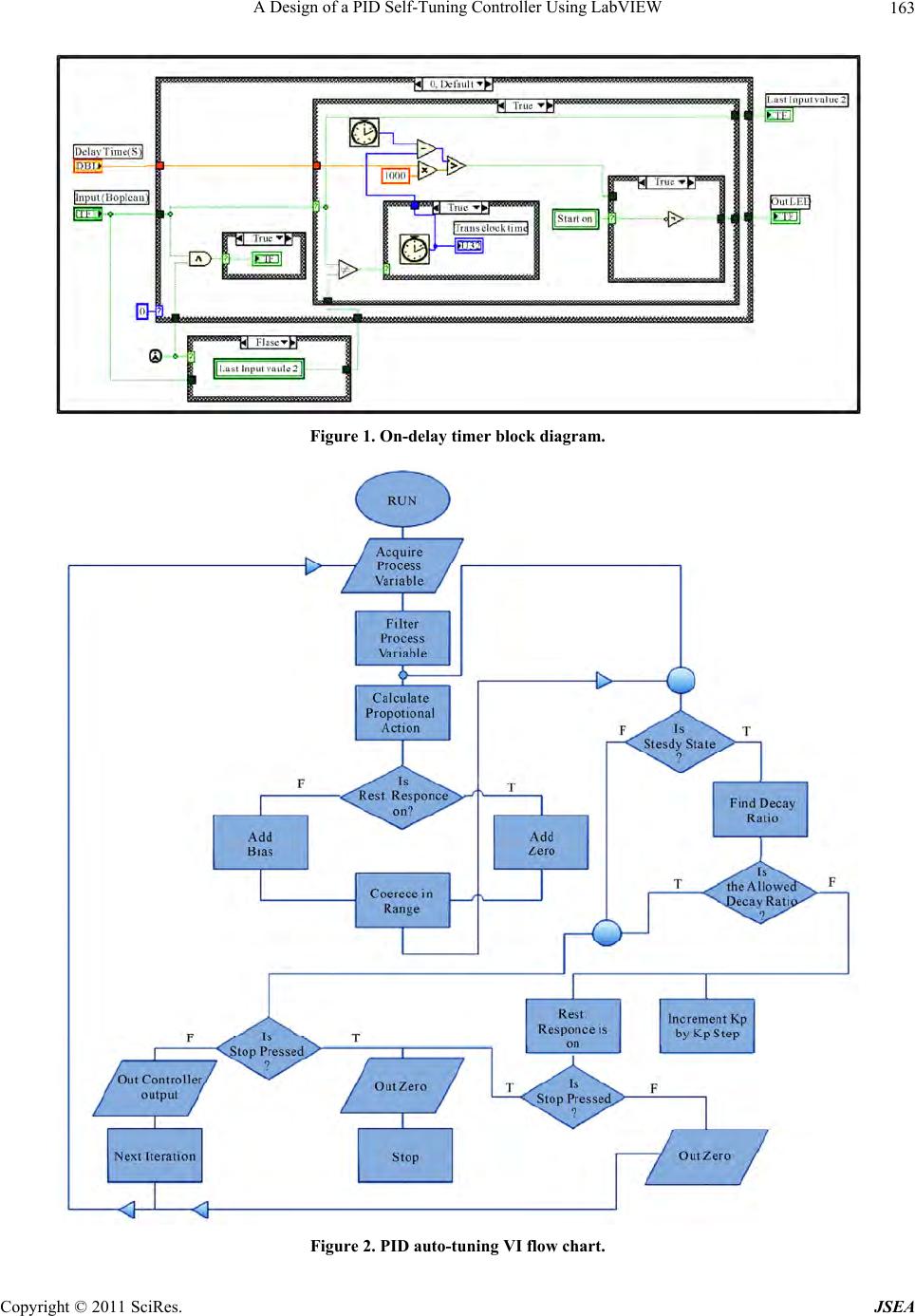
Pillai (2017) pointed out that There are four main ways for adaptive controlling Gain scheduling, Model Reference adaptive controller, Dual control, Self-Tuning regulators. Adaptive controller monitors the performance and make adjustment. Adaptive controller is an approach for such systems.
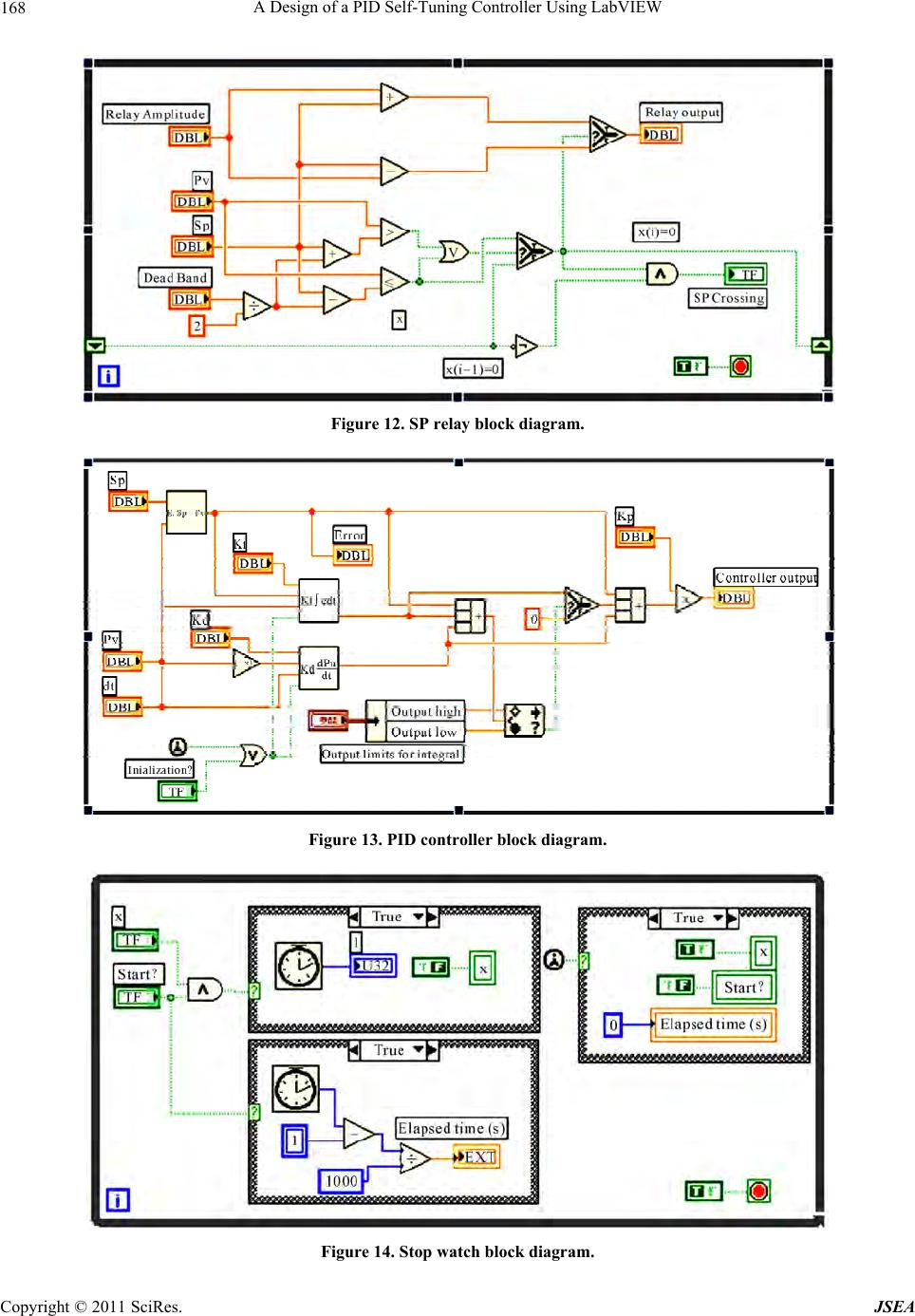
At least three parameters need to be adjusted and an experienced engineer is therefore required for practical tasks, but Andeescu (2008), Tang (2003) and Lee (2006) have proposed that it always occurs that the improperly adjusted parameters cause unsatisfactory system response. Unknown inertial parameters may be carried in the industrial equipment while not easy to estimate. However, these classical PID controller are not flexible for the parametric changes and are limited in some application in practice that may have varying parameters. Three parameters need to be set in the system and many means of parameters calculation are used, such as trial-error, loop-shaping, Bode, and Nyquist (Andeescu 2008). Each-loop can be adjusted by a cascade controller.
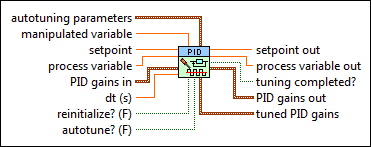
Commonly used control strategy of DC motor speed is classical Proportional Integral Derivative (PID) controller (Sul 2011). For all these applications, precise speed control is necessary and is directly related to the performance of products.ĭC motor speed is controlled either by changing armature current or changing resistance in armature circuit or field circuit (Balamurugan 2020). As many researches showed (Lee 2020, Mai 2015) that DC motor has been widely adopted in industry control area, such as 3D-printers, mobile robots, electric vehicles and household machines. DC Motor transforms electricity energy to mechanical energy and has good characteristics of good starting, speed regulation performance, and simple design.
